Available to Ship1
|
-
Contact your local sales office. This Item cannot be cancelled or returned.
|
Product Line
|
-
VEXTA®
|
Motor Type
|
-
5-Phase
|
Frame Size
|
-
2.36 in
|
Motor Length
|
-
3.48 in.
|
Speed-Torque Characteristics
|
-
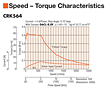 Speed - Torque Characteristics
|
Holding Torque
|
-
59 oz-in
|
Type
|
-
Standard
|
Shaft/Gear Type
|
-
Round Shaft (No Gearhead)
|
Electromagnetic Brake
|
-
Equipped
|
Shaft
|
-
Single
|
Power Supply
|
-
24 VDC
|
Current
|
-
2.5 A
|
Basic Step Angle
|
-
0.72º
|
Rotor Inertia
|
-
1.83 oz-in²
|
RoHS Compliant
|
-
Yes
|
Safety Standards
|
-
CE
|
CE Marking
|
-
EMC Directives
|
Components
|
-
PK564AWM (Motor) CRD514-KP (Driver)
|
Insulation Resistance
|
-
[Motor] 100 MΩ or more when 500 VDC megger is applied between the windings and the case under normal ambient temperature and humidity.
|
Dielectric Strength
|
-
[Motor] Sufficient to withstand 1.5 kVAC at 50 Hz or 60 Hz applied between the windings and the case for 1 minute under normal ambient temperature and humidity.
|
Dielectric Strength (Driver)
|
-
[Driver] Sufficient to withstand the following for 1 minute under normal temperature and humidity: FG terminals – Power input terminal - 500 VAC, 50 or 60 Hz
|
Insulation Class
|
-
[Motor] Class B [266ºF (130ºC)], Recognized as Class A 221ºF (105ºC) by UL standard
|
Ambient Temperature Range
|
-
[Driver] 32ºF ~ 104ºF (0ºC ~ 40ºC) (nonfreezing) [Motor] 14ºF ~ 122ºF (-10ºC ~ 50ºC) (nonfreezing)
|
Ambient Humidity
|
-
85% or less (noncondensing)
|
Operating Atmosphere
|
-
No corrosive gases, dust, water or oil.
|
Temperature Rise
|
-
[Motor] Temperature rise of the coil measured by the Change Resistance Method is 144ºF (80ºC) or less (at rated current, at standstill, five phases energized).
|
Shaft Runout
|
-
0.002 in (0.05 mm) T.I.R. at top of output shaft
|
Concentricity
|
-
0.003 in. (0.075 mm) T.I.R.
|
Perpendicularity
|
-
0.003 in. (0.075 mm) T.I.R.
|
Stop Position Accuracy
|
-
±5 arc minutes (±0.084º)
|
Radial Play
|
-
0.001 inch (0.025 mm) max. of 1.12 lb. (5 N)
|
Axial Play
|
-
0.003 in (0.075 mm) max. of 2.2 lb. (10 N)
|
Radial Load
|
-
0 in. from Shaft End = 14.1 lb0.2 in. from Shaft End = 16.8 lb0.39 in. from Shaft End = 21 lb0.59 in. from Shaft End = 29 lb0.79 in. from Shaft End = 42 lb
|
Axial Load
|
-
4.5 lb
|